|
|
FAQs |
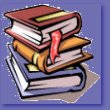
This page is about Frequently Asked Questions about powder
coating. You are invited to add your contributions to this page.
|
The
FAQs about Powder Coating.
What Is Powder Coating?
Why doesn’t powder coated parts drip or run in the oven?
What are Advantages and disadvantages of powder coating
Is it hard to learn to powder coat?
How much does powder coating cost?
Is there any dangers with mobile phones been around powder spray booths?
How long does Powder Coating typically last?
How many Powder Coat colors are there?
How many coats are applied with powder coating?
Can powder coatings be applied on site?
How are powder coatings manufactured?
What is the correct procedure for disposal of powder coatings?
The Future of Powder Coating?
---------------------------------------------------------
What Is Powder Coating?
The powder coating process uses a solvent free dry mix of plastic
resins, pigments and fillers that melt and fuse together when heated.
The main difference between a conventional liquid paint and a powder
coating is that, the powder coating does not require a solvent to keep
the binder and filler parts in a liquid suspension form. The coating is
typically applied electrostatically and is then cured under heat to
allow it to flow and form a "skin." The powder may be a thermoplastic or
a thermoset polymer. It is usually used to create a hard finish that is
tougher than conventional paint. Powder coating is mainly used for
coating of metals, such as "white goods", aluminium extrusions, and
automobile and motorcycle parts. Newer technologies allow other
materials, such as MDF (medium-density fibreboard), to be powder coated
using different methods. The solid particles of coating are
electrostatically charged in a spray gun and carried by low velocity air
to the surface of the piece to be coated. The electrostatic charge holds
the powder particles in place while the part is cured in a 200 degree C.
The heat of the oven causes a chemical reaction to occur and the powder
to cure, creating a highly durable finish
Back To Top
Why doesn’t powder coated parts drip or run in the oven?
When powder is in the "gel state" it is very thick like paste and
therefore, it doesn’t run or drip.
Back To Top
What are Advantages and disadvantages of powder coating
There are several advantages of powder coating over conventional liquid
coatings:
Powder coatings emit zero or near zero volatile organic compounds (VOC).
Powder coatings can produce much thicker coatings than conventional
liquid coatings without running or sagging.
Powder coating overspray can be recycled and thus it is possible to
achieve nearly 100% utilization of the coating.
Powder coating production lines produce less hazardous waste than
conventional liquid coatings.
Capital equipment and operating costs for a powder line are generally
less than for conventional liquid lines.
Powder coated items generally have fewer appearance differences between
horizontally coated surfaces and vertically coated surfaces than liquid
coated items.
A wide range of specialty effects are easily accomplished using powder
coatings that would be impossible to achieve with other coating
processes.
Back To Top
Is it hard to learn to powder coat?
Almost anybody can learn to apply powder with consistent thickness
build and minimum waste.
One area that is not hard to learn, but often skipped over, is cleaning
and preparing the substrate to accept the powder. We spend a lot of time
and energy in this area. If you don't get this right, the rest is wasted
effort. Put your brain to work here, you'll be glad you did.
Back To Top
How much does powder coating cost?
Powder coating costs about the same as other professionally applied
paints or coatings. Some bulk plating processes similar to anodizing may
be slightly less expensive. More decorative finishes like chrome plating
is substantially more expensive than powder coating.
Back To Top
Is there any dangers with mobile phones been around powder spray booths?
Whilst powder coatings have the advantage over solvent based coatings of
having a lower explosion point and therefore is less flammable, caution
should always be exercised with any electrical source such as mobile
phones. Powder coating is a fine organic dust which in high
concentration, in the presence of air and an ignition source such as a
mobile phone, could trigger a dust explosion.
The concentration of dust required to facilitate a dust explosion is
significant, however, it is advisable to keep unnecessary equipment away
from the booth and powder store. As a precaution, all mobile phones
should be kept clear of these areas.
Back To Top
How long does Powder Coating typically last?
This is a very common question. From the perspective of adhesion and
film integrity, correctly applied and pretreated powder coated metal can
and has lasted since it was first applied more than 30 years ago.
Powder coatings are considered extremely resilient, be a coating of
choice for use on gas or oil pipelines which are buried in the earth or
underwater. Powder coatings are used on automotive and appliances given
their excellent chip resistance, hardness and or chemical resistance.
From the perspective of resistance to light and UV degradation, some
powder coatings are outstanding, being used on major building such as
Duratec and Fluoroset FP.
The standard and most common powder coatings are designed for general
use and applications. Standard powder coatings offer good weathering
resistance, excellent film integrity and very good hardness.
Back To Top
How many Powder Coat colors are there?
There are about 100 different colors on a regular basis, but there are
several thousand available . And, if money is no object, there is no
limit to what’s available.
In addition to the different colors and shades, Powder Coat is available
in several “Finish Types”. They are classied as Texture (aka Hammertone),
Metallic (like metal flake it comes in several sizes of “Flakes” from
large to micro), Solid, Translucent (aka ‘Candy’) and Clear (actually a
Clear Translucent). and a fairly new one known as “Chrome”,
Back To Top
How many coats are applied with powder coating?
Powder coatings are generally a one coat finish, applied to suitable
cleaned and pretreated substrates. Some coatings, such as metallics,
require a clear coat to protect the metallic effect.
Back To Top
Can powder coatings be applied on site?
Powder Coatings are a factory applied finish using specialised
equipment. The equipment includes an electrostatic spray gun, spray
booth and an oven to bake (or cure) the coating. On site application is
not possible given the hot curing cycle required to fuse the coating.
Back To Top
How are powder coatings manufactured?
Powder Coatings are produced by dry blending of resins, pigments,
additives and curing agents, which are then extruded at elevated
temperatures to melt mix the ingredients. The material then becomes
thick and viscous like a honey mixture which is cooled using super
chilled water, before the material is crushed progressively to a fine,
well defined particle size. Specialised equipment including rotary
sieves and particle size measuring equipment is used to monitor and
control the particle size distribution.
Back To Top
What is the correct procedure for disposal of powder coatings?
The rules and regulations for powder waste disposal vary across country.
In many instances, powder coating is suitable for land fill, however it
is important to contact Environmental Protection Agency offices to
clarify local requirements for waste disposal.
Back To Top
The Future of Powder Coating?
In addition to successfully penetrating the MDF (medium density
fiberboard) market, powder has proven to be an effective finishing
choice for other heat sensitive substrates such as plastic parts made of
nylon and polycarbonate and assembled or partially assembled products
such as appliances, electric motors or automotive radiators. Because of
advancements in low temperature cure powders, plastic parts and wires
and rubber seals and gaskets are not damaged in the powder coating
process.
And the revolution has just begun. Successful testing has occurred on
hardwoods such as beech, oak, ash and walnut. Research engineers are
studying the use of powder on paper-laminated MDF, laminated flooring
and particleboard. Research is also being conducted on countertops, wood
moulding and trim, all of which will increase demand for, and use of,
powder coatings in more new markets
Back To Top
|
|
|
|